Ceramic sink, which seems ordinary in our daily life, but indispensable object. From raw material selection to high-temperature firing, the ceramic sinks production process involves molding, drying, and glazing. Enter the bathroom ceramics manufacturer’s ceramic sink factory, let’s take a look at the production process of ceramic sinks.
Material selection stage.
The journey of making ceramic sinks begins with the careful selection of raw materials. High-quality terracotta and China clay, like sleeping treasures, are excavated from the depths of the earth by experienced artisans. These soil materials need to be rigorously screened to remove impurities, leaving only fine and pure parts. They are then fed into giant grinding machines where they are repeatedly crushed and pulverized into tiny particles. These particles then mix with just the right amount of water to create a silky, silky mud. In the process of mixing, the mud seems to have life, constantly churning and surging. At this time, craftsmen will add various minerals and additives according to the formula to give the ceramic sink unique properties and texture.
Molding of Ceramic Sinks Production Process
This can be done in a variety of ways, such as mold grouting or machine pressing. Mold grouting is injecting mud into a special mold and using the shape of the mold to shape the basin. Machine pressing can achieve efficient mass production and ensure product consistency.
Sand and dry.
After forming the body is still very fragile and rough, and needs to be carefully polished and trimmed by workers, and then wipe the debris on the surface with water to make the body more smooth. After a period of drying, the temperature and humidity in the drying chamber are precisely controlled to ensure that the water in the billet evaporates evenly and slowly. This process is like a delicate balance, neither too fast to cause the body to crack nor too slow to affect the production schedule.
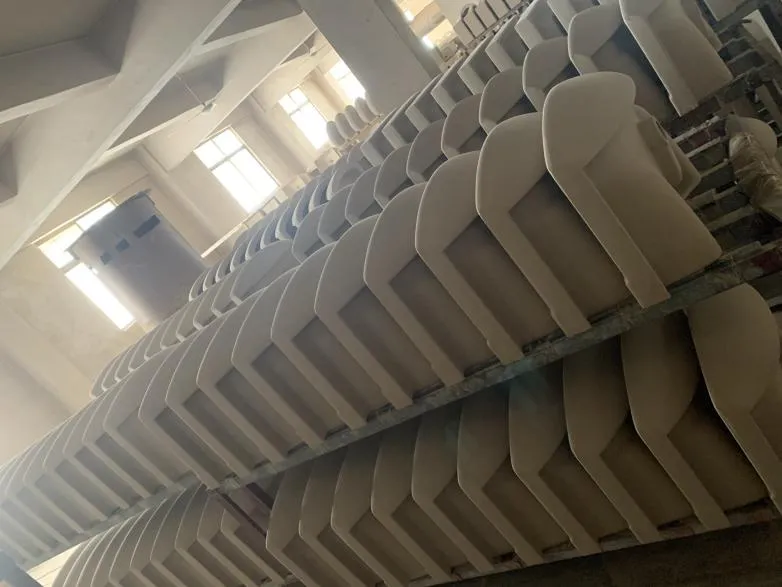
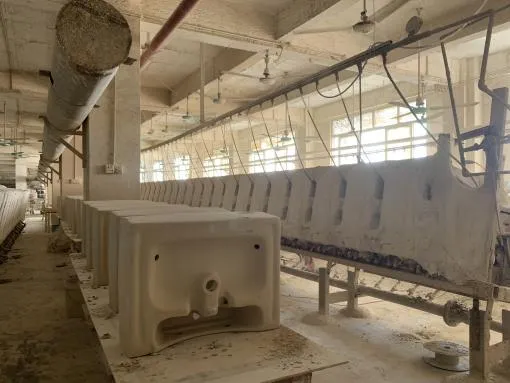
Check and glazing.
After drying the body, it is also necessary to use kerosene to check whether there is a cracking place, and then wipe with water again, and then arrange to spray glaze, according to the needs of customers can customize the color of the glaze, including bright white, bright black, matte white, matte black and so on.
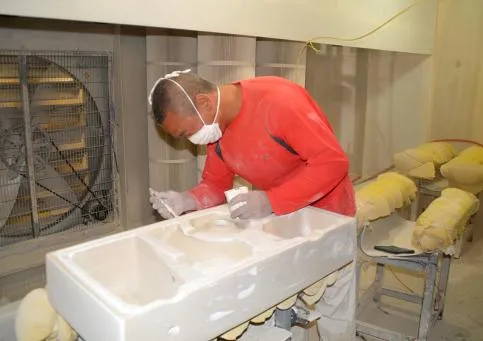
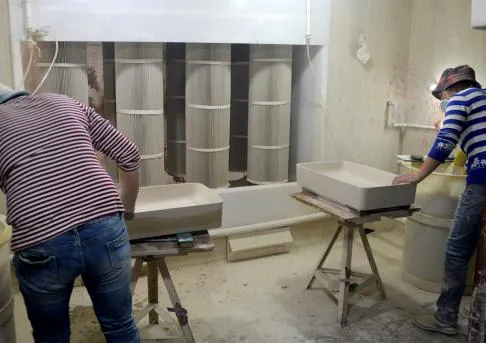
High-temperature firing.
The dried body is sent to a high-temperature kiln for firing. The temperature in the kiln is as high as 1280℃, and the billets undergo drastic physical and chemical changes in such a high-temperature environment. To reduce energy consumption and exhaust emissions, the factory uses an energy-efficient kiln and is equipped with an advanced waste gas treatment device to purify the waste gas generated during the firing process, so that it meets environmental protection standards.
In the process of firing, the use of glaze is a key link. The glaze is like the costume of the ceramic sink, adding a bright color and smooth texture to it. Under the action of high temperature, the glaze melts and evenly covers the surface of the basin body, forming a layer of transparent or colored protective film.
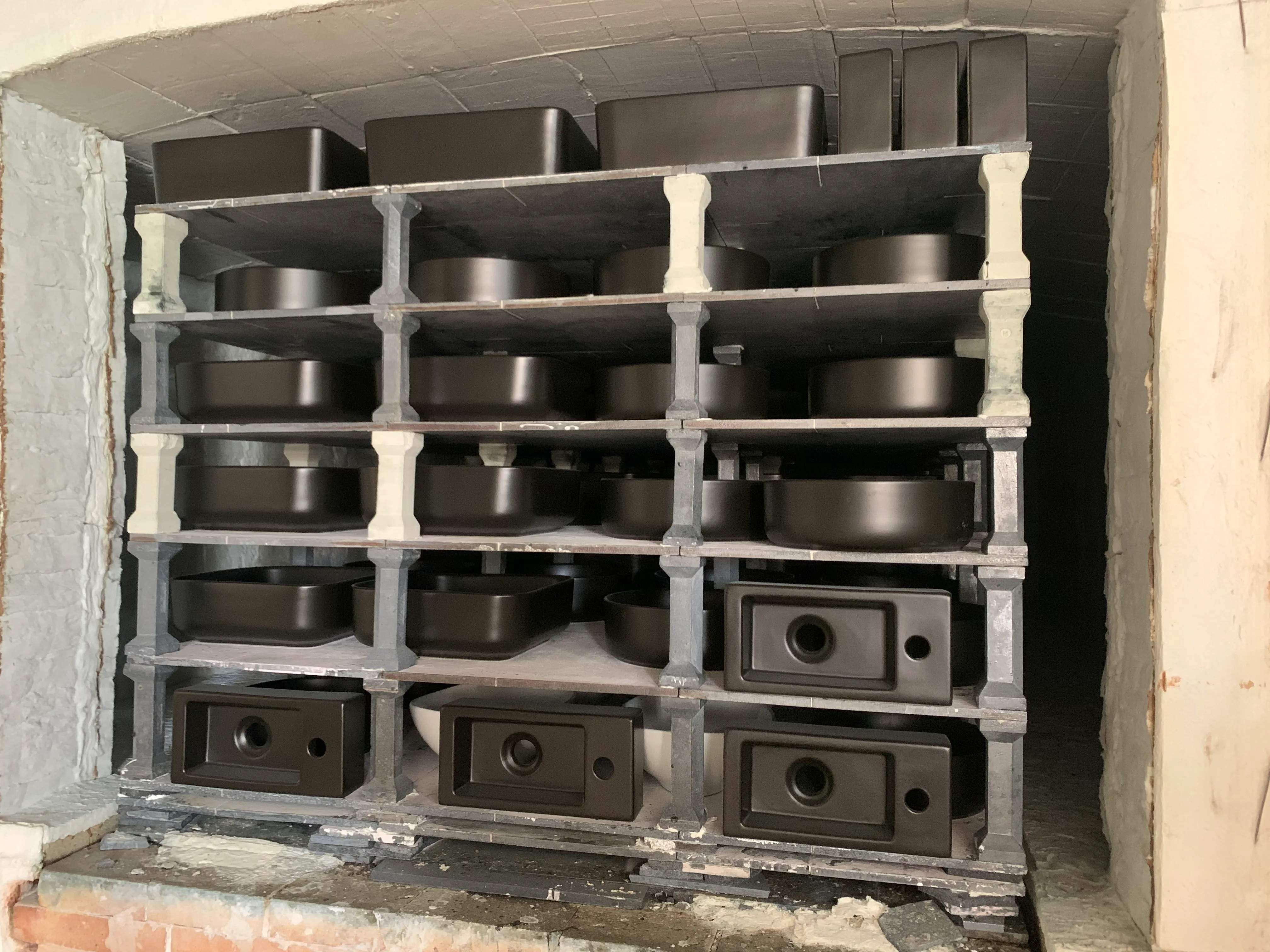
However, in this entire production process, the concept of environmental protection has always been throughout. The factory adopts advanced dust collection equipment, and for the wastewater generated in the production process, the factory is equipped with an efficient sewage treatment system, which removes harmful substances in the wastewater through a series of physical, chemical and biological treatment methods, so that the treated water meets the discharge standards, can be recycled or safely discharged.
Inspection and repair.
After the firing is completed, the ceramic sink needs to be inspected and trimmed. The workers carefully examine each basin to see if there are any defects, distortions, or uneven colors. For products with small defects, they will be carefully trimmed and polished to ensure that their quality is up to standard.
After this series of complex and fine processes, an exquisite ceramic sink finally appeared in front of our eyes. It is not only a practical daily necessity, but also the crystallization of the wisdom and efforts of craftsmen, carrying the inheritance and innovation of traditional crafts, as well as the responsibility for environmental protection. It will enter thousands of households, add a warm and beautiful to people’s lives, perhaps will enter a warm family, and become a beautiful scenery on the washing table; May appear in a luxury hotel, to provide guests with comfortable service.
The production process of ceramic sinks is not only the inheritance of traditional technology, but also the perfect combination of modern science technology and art, but also the active practice of the environmental protection concept. Every link is poured into the craftsmen’s effort and wisdom so that this ordinary ceramic sink has extraordinary value.
The technical difficulties of ceramic sinks production process
Raw material control
- Ensure the purity, particle size and stability of the chemical composition of the raw material, which has an important impact on the quality and performance of the ceramic sink.
- Raw materials may vary from origin and batch to batch and need to be precisely prepared to maintain product consistency.
Molding process
- When the mold is grouting forming, the design and production accuracy of the mold are directly related to the dimensional accuracy and surface quality of the product, and the bubbles and defects in the process of grouting should be avoided.
Drying control
- During the drying process, if the temperature, humidity, and time are not properly controlled, it can easily lead to cracking and deformation of the billet, affecting the yield.
Firing process
- It is important to achieve the right firing temperature and holding time, too high or too low temperature will affect the physical properties and appearance quality of ceramic sinks.
- Temperature uniformity in the kiln is also a challenge to ensure that each ceramic sink gets an even firing.
Glaze application
- The glaze formula and the thickness and uniformity of the glaze will affect the appearance and waterproof performance of the ceramic sink.
- The combination effect of glaze and blank body in the firing process needs to be precisely controlled, otherwise there may be problems such as glaze cracking and peeling.
Dimensional accuracy
- To meet strict dimensional tolerances, especially in mass production, to ensure that the size of each ceramic sink can meet the standard for easy installation and use.
Quality inspection
- Effective detection of subtle internal defects and potential problems such as pores, hidden cracks, etc., requires advanced inspection equipment and technology.
Ceramic Manufacturers Association brings together many reliable Ceramic sink manufacturers who can provide you with high-quality Ceramic Bathroom Sinks quickly and efficiently, demonstrating our superior ceramic sinks production processes and strict quality control.