As a key piece of equipment in production, tunnel kilns play an important role in improving product quality and productivity in home ceramics factories. This article will explain how tunnel kilns work, their advantages over conventional kilns, and why the ceramic manufacturers of the Chaozhou Ceramic Manufacturers Association place a high value on the use of tunnel kilns.
what is tunnel kiln?
A tunnel kiln is a continuously operated kiln, usually in the shape of a long tunnel, with the interior divided into a preheating zone, a firing zone and a cooling zone. The firing of the product takes place in the central part of the tunnel. The ceramic bodies to be fired enter the kiln continuously through a long horizontal conveyor belt, passing through different temperature zones in turn to complete the firing process.
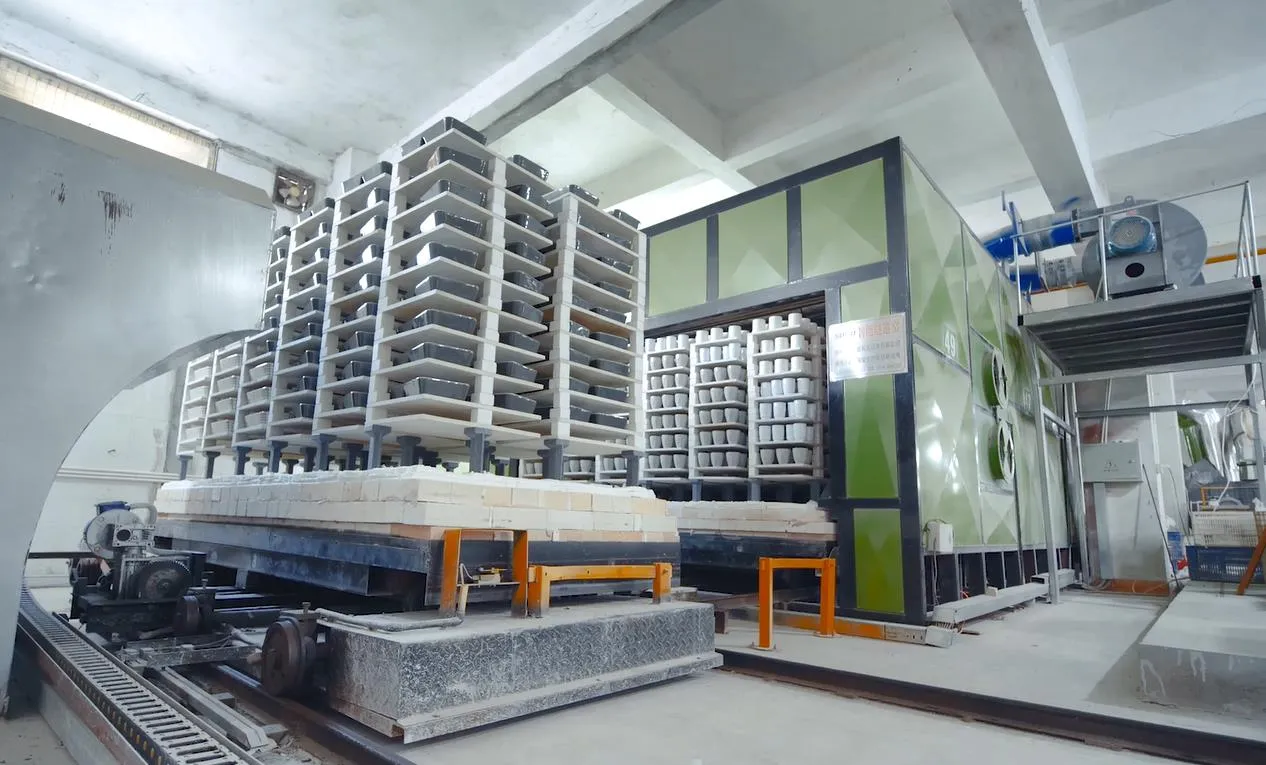
Operating principle of tunnel kiln
- Preheating zone: After the ceramic products enter the kiln, they are first heated in the preheating zone. This stage is mainly to drive away moisture and organic matter, and at the same time prepare for firing.
- Firing zone: In the firing zone, the temperature reaches the highest, and the body of the ceramic product is sintered and formed at this stage, and finally densification and crystal phase transformation are completed, which is the key stage of ceramic firing.
- Cooling zone: After firing is completed, the ceramic product enters the cooling zone and gradually cools down to room temperature to form the final physical and chemical properties.
The main advantage of tunnel kiln technology is that it can fire a variety of ceramic products and better control the firing process and the high quality of the product. Tunnel kilns are widely used in large-scale ceramic production due to their high efficiency, energy saving and high degree of automation.
Application of tunnel kilns in household ceramic factories
Tunnel kiln technology was developed in Germany in the mid-19th century and was initially used for firing bricks. After World War II, the technology was widely adopted. In Asia, China and Vietnam began to adopt the technology in the 1970s, and hundreds of tunnel kilns are now in operation.
Chaozhou is a famous center of the household ceramics industry in China and even in the world, where many ceramics manufacturers are gathered and tunnel kiln technology is widely used. As an advanced kiln equipment with high efficiency, energy saving and a high degree of automation, the tunnel kiln not only improves the quality and production efficiency of household ceramic products but also greatly reduces energy consumption and exhaust emissions.
Tunnel kiln vs. traditional kiln: Why did we choose tunnel kiln?
In ceramic production, the choice of kiln has a crucial impact on product quality, production efficiency and environmental protection. With the continuous advancement of technology, tunnel kilns have gradually become the mainstream choice to replace traditional kilns. The following is a comparative analysis of tunnel kilns and traditional kilns, and why we chose tunnel kilns.
Production efficiency
Traditional kilns: Traditional kilns are usually intermittent operations, that is, a batch of products needs to be fired before the next batch of production can be started. This method limits production efficiency, especially when facing the large-scale production needs of household ceramics, it is difficult to meet the efficient production requirements.
Tunnel kiln: Tunnel kiln adopts a continuous production mode, and the ceramic embryos are continuously entered into the kiln through kiln cars or conveyor belts, and gradually complete the preheating, firing and cooling processes. This process not only greatly improves production efficiency, but also enables 24-hour uninterrupted production to meet the production needs of large quantities of household ceramics.
Temperature control and product quality
Traditional kilns: In traditional kilns, temperature control is relatively difficult to achieve uniform distribution. Due to the inconsistent temperature of each part, the product is prone to uneven firing, deformation or cracking, resulting in unstable quality of household ceramic products.
Tunnel kiln: The tunnel kiln has a precise temperature control system that can set different temperatures in different areas of the kiln to ensure that each ceramic product is evenly heated throughout the firing process. This precise control not only reduces the production of defective products, but also improves the overall quality and consistency of our household ceramic products.
Energy saving and environmental protection
Traditional kilns: Traditional kilns have low fuel utilization rates, usually generate a lot of energy consumption and exhaust emissions, and have a greater impact on the environment. At the same time, due to the large loss of heat energy, the production cost is relatively high.
Tunnel kiln: Tunnel kilns use advanced heat recovery technology and efficient combustion systems, which can greatly reduce energy consumption and reduce production costs. In addition, tunnel kilns also perform well in exhaust gas emission control, meet modern environmental protection requirements, and reduce the impact on the environment.
Degree of automation
Traditional kilns: Traditional kilns rely on a lot of manpower operations, have a low degree of automation, and the operation process is complex and error-prone, which also increases labor costs and the chance of errors.
Tunnel kiln: Tunnel kiln is usually equipped with advanced automatic control system, including temperature monitoring, kiln car operation control, etc., which can realize precise operation with less human intervention. This not only reduces labor intensity, but also improves the stability and safety of our ceramic factory production.
Production flexibility
Traditional kiln: Due to the intermittent operation characteristics of traditional kilns, it is difficult to adjust and switch when producing different types of ceramic products, and the flexibility is poor.
Tunnel kiln: The design of tunnel kiln is more flexible, which can adapt to the firing needs of ceramic products of different types and sizes, and the adjustment operation is more convenient, so as to better meet the diversified needs of the market. This is also the reason why Jinhua can produce any type of household ceramic products and maintain stable quality.
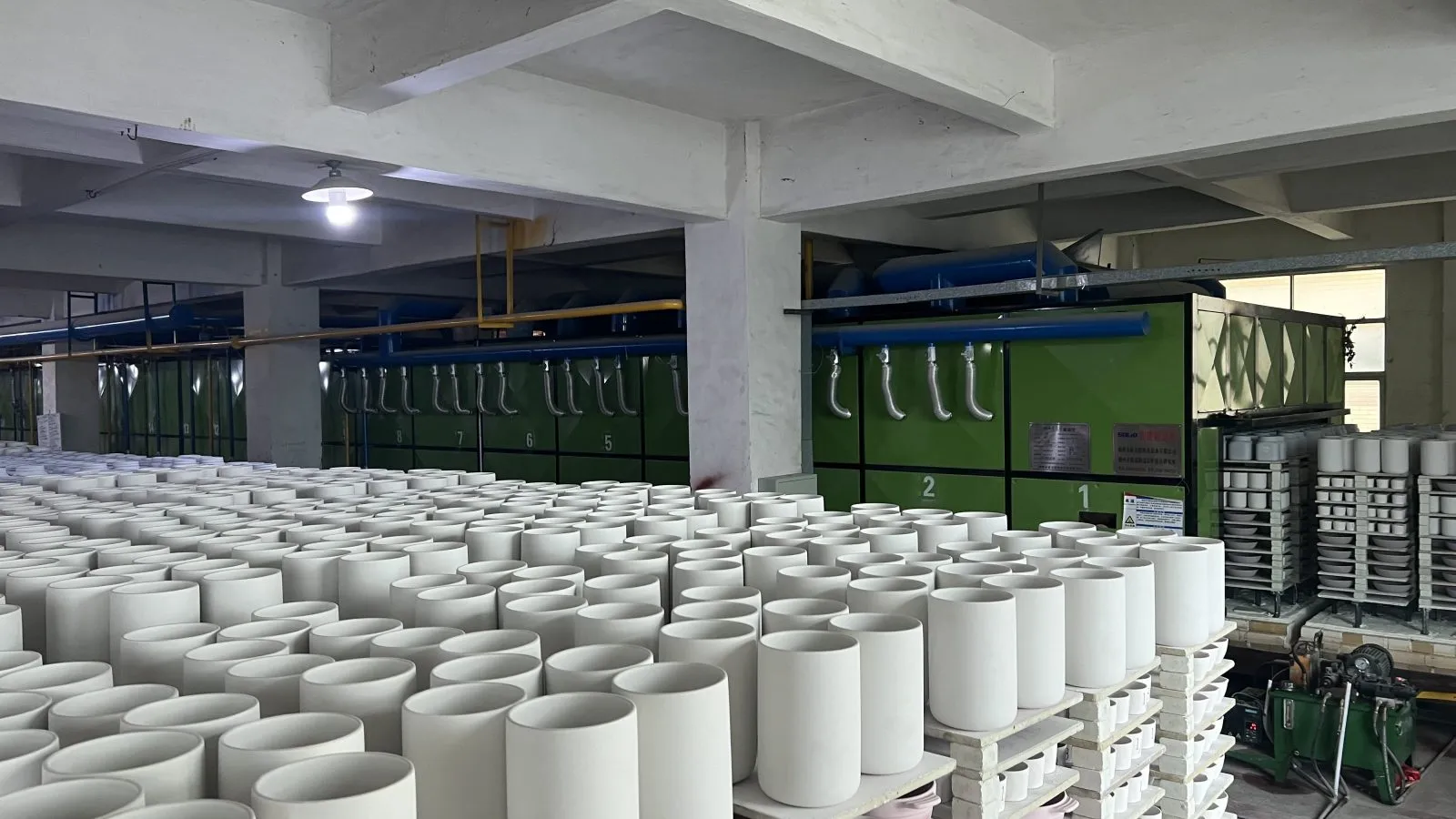
Production advantages of tunnel kilns
Continuous production
Tunnel kilns allow ceramic products to move continuously in the kiln, thereby achieving continuous firing in large quantities. This continuity improves production efficiency and is suitable for the large-scale production rhythm of the household ceramic industry.
Accurate Temperature Control
The temperature inside the tunnel kiln is clearly divided into zones, and the temperature of each zone can be controlled independently, which helps to optimize the firing curve and ensure the stable quality of our household ceramic products.
Significant Energy-saving Effect
Tunnel kilns are usually equipped with advanced combustion and heat recovery systems, which can effectively reduce energy consumption. At the same time, the design of the airflow in the kiln helps to evenly distribute heat and improve thermal efficiency.
Stable Product Quality
Due to the stable and precise control of the temperature in the kiln, the tunnel kiln can ensure the uniformity of the firing of our household ceramic products, reduce defects caused by temperature fluctuations, and improve product consistency and qualified rate.
High Degree of Automation
Modern tunnel kilns are usually equipped with automated control systems, including temperature monitoring, kiln in and out control, etc., which makes the production process more intelligent and reduces the complexity of manual operation.
Summarize
We chose the tunnel kiln precisely because it performs well in terms of production efficiency, product quality, energy conservation and environmental protection, automation and production flexibility.
As a household ceramics manufacturer pursuing excellence and sustainable development, the application of tunnel kilns allows us to maintain a leading position in the highly competitive market while also better serving the needs of global customers.
The Ceramic Manufacturers Association also actively promotes tunnel kiln technology, encouraging member companies to adopt this efficient and environmentally friendly production method, and jointly drive the industry towards higher quality and sustainable development.
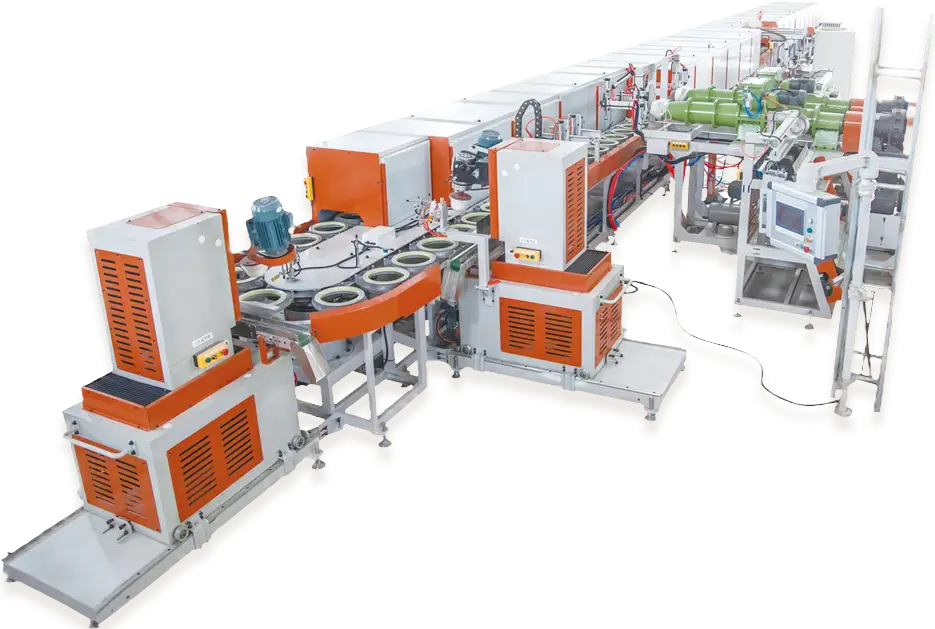